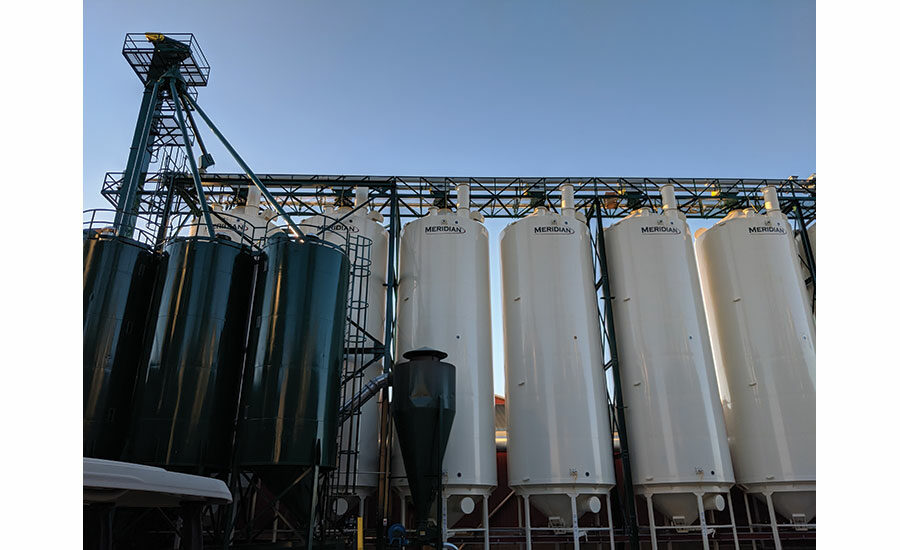
C&M Seeds turns to Luxme for conveying solution
Dust control, durability and maintenance concerns were key criteria
C&M Seeds is a small but significant Canadian supplier of red wheat genetics and marketer of soybeans, barley, oats and mixed grains. When the company undertook a 30% storage capacity expansion project to its primary facility, a sealed, top-of-silo handling conveyor was required to meet growing business demand.
C&M Seeds outlined dust control, durability and easy maintenance as key criteria for the transportation system at its Palmerston, Ont., seed processing facility. The capability to withstand harsh environments and eliminate the risk of cross-contamination between seed batches was important.
After receiving proposals from a number of machinery developers, the company chose Luxme’s automated tubular chain conveyor with Stay Clean technology. “Our project team, operators and management felt this was the best option to achieve our need for very high-quality operations,” says Rob McLaughlin, sales and marketing manager, C&M Seeds.
Removing risk of cross-contamination
As a supplier to more than 200 seed retailers and farmers across eastern Canada and beyond, C&M Seeds needed to improve the process of transferring finished batches to one of eight silos while maintaining the highest standards of quality. As a certified seed producer, the firm earned its reputation and accreditation by following a rigid set of quality control standards set out by Canada’s Plant Breeders’ Rights (PBR) Act. To eliminate the risk of cross-contamination, these standards must be maintained when transporting the company’s seed species—including winter wheat, spring wheat and soybean—to the silo for storage. The challenge was achieving this with one machine.
“Our business depends on supplying 100% pure seed stock; just one kernel can contaminate a batch, which we work very hard to avoid,” McLaughlin explains. “Any contaminating variety of seed will create serious complaints and lead to significant losses for the retailer.”
Luxme’s system ensures a clean operation without cross-contamination between seed batches due to its self-cleaning technology. A chain disc tipper, disc cleaning brush station and wiper discs clean out and purge the machine of any product, before operators inspect the interior for any visible residue after each batch.
McLaughlin says, “As the machine runs, it cleans itself and purges any random seeds. These are cleaned off the equipment and delivered back to the designated silo they were initially intended for. Also, we have noticed that there is no additional damage to the seed after the cleaning process.”
The self-cleaning technology has reduced maintenance costs and contributed to higher ROI. Since installation in June 2019, McLaughlin reports the company has saved two hours of washdown labor time between each batch. “We have had to service the system much less frequently than other equipment and technology we have used in the past,” he says.
For all seasons
In addition to eliminating the potential for cross-contamination, protecting the product from external influences was also crucial for C&M Seeds. Since the conveyor is required to operate over 78-ft.-high silos throughout the four Canadian seasons, consistent performance with minimal maintenance were important factors due to the associated cost and difficulty of servicing equipment at a high elevation.
The conveyor needed to run clean without carry-over and operate reliably outdoors with minimal service. It had to be insensitive to weather conditions and deliver worry-free operation 12 months a year. Rather than commissioning an off-the-shelf unit, the Luxme team collaborated with C&M Seeds to engineer a unique transportation solution. Designed for high reliability, the conveyor runs with minimal power consumption at 7.5 hp with full load start and stop capabilities. It operates quietly as it transfers product to any one of six electrically operated, high efficiency Luxme rotary valves, which direct segregated and cleaned seed batches to any of the eight new storage silos.
The tubular chain conveyor now performs at capacity with a throughput of 21,000 bushels per hour, receiving material from a bucket elevator that transfers the seed vertically to the top of the silos. Using a VFD drive, operatives can increase or decrease speed as necessary, allowing the conveyor to match the speed of the cleaner at the final stage before storage.
Beyond low maintenance and efficient and effective process flow, it was imperative for the wellbeing of C&M Seeds’ workforce to remove the need for regular high-risk, outdoor servicing. “The conveying solution from Luxme has allowed us to significantly reduce our hazardous, elevated work practices; much to the benefit of our employees,” McLaughlin says. “We have noticed the operation is worry-free. All we have to do is set the speed at the start of the batch and just let it run. The C&M Seeds team is extremely satisfied with the innovation and support provided by Luxme for this important step in our expansion process.”