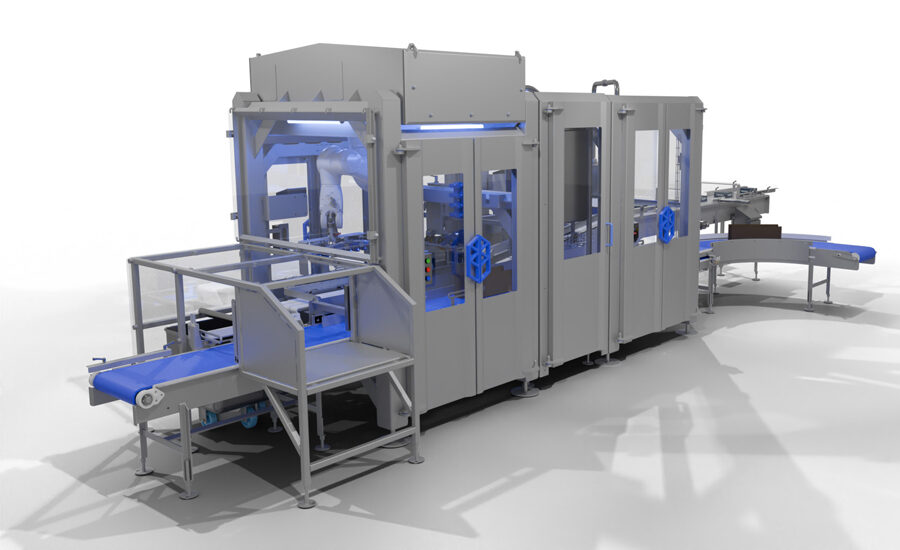
Designing an Automated Case-Packing Solution
In food processing, automating case packing has become crucial as labor shortages and rising costs push companies to seek efficient alternatives. Case packing, the process of placing packaged products into a box for shipping, has been used in industrial settings for years. With new advancements making machines smaller and washdown-capable, food processors are increasingly adopting automated systems.
Case Packing vs. Carton Loading
Sponsored by
Understanding the difference between case packing and carton loading is essential. Case packing involves packaging items into a box for transport, often before the products are stocked at a retail location. Carton loading, on the other hand, puts products into containers that go directly to store shelves. Cartons are frequently packed into cases for shipping.
While automated case packing is common in industrial processing, it’s only recently gained traction in food processing due to advancements in technology and the need to counter rising costs. Companies are adopting automation to streamline operations, particularly to enhance speed and efficiency.
Design Considerations for Automated Case Packing
The design of an automated case-packing solution hinges on several factors, including case design. Processors choose specific case sizes and styles based on the product to optimize palletization, ensuring minimal empty space and preventing damage during transport. For example, meat processors may use clamshell boxes to avoid sagging when pallets are stacked.
How products are loaded into cases—whether from the top, bottom, or sides—is also an important design consideration. Additionally, processors establish a pallet pattern that maximizes the number of cases on a pallet without exceeding weight or size limitations. The case-packing solution must be able to load and arrange these cases quickly and efficiently to avoid production delays.
Many case-packing operations are performed away from primary food handling areas, meaning the equipment doesn’t always need to be washdown capable. However, food processors who do require this level of sanitation previously faced limitations until Stäubli introduced washdown-capable, food-grade robots that can be cleaned with hot water and chemicals.
Handling Multiple SKUs
Case-packing solutions must be flexible enough to handle multiple SKUs (Stock Keeping Units). Different products require different case sizes, so systems must adjust quickly to accommodate changes. Frequent changeovers can cause downtime, so it’s critical that the case-packing solution minimizes these interruptions. Although there’s no strict limit on the number of SKUs a system can process, the more complex the variety, the more time and effort changeovers may require. In some cases, processors opt to invest in multiple machines to handle the variety of SKUs more efficiently.
The Drive for Automation
Processors turn to automation primarily for speed. Automated case packers allow facilities to pack and palletize more cases in less time, reducing bottlenecks and increasing throughput. Any delays in case packing can slow down production, which affects shipping and revenue.
Robots are typically required to achieve high speeds, but this increases the system’s footprint, making space a concern for many processors. Smaller machines, while helpful, often can’t meet the desired speed for high-volume operations. For processors without the necessary space, manual labor remains the fallback option.
Challenges in Automation
Automating case packing isn’t without its challenges. In some situations, human packers are still better at squeezing or manipulating products into cases, especially when space is tight. This type of dexterity can be difficult for robots to replicate at high speeds, leading processors to rethink case sizes or product quantities to better suit automation.
Additionally, product orientation is crucial. To maximize pallet space and protect products during shipping, some processors must reorient products before they’re packed, which may require cameras to guide the robotic arms. Choosing the right end-of-arm tooling (EOAT)—whether grippers, vacuum tools, or mechanical arms—is also essential to ensure the system handles the products effectively.
EnSight Solutions: Compact and Efficient Case-Packing
EnSight Solutions has developed an innovative, space-saving case-packing system in response to industry demands. Many food processors lack the floor space for traditional, large-scale automation systems. EnSight’s compact, washdown-capable solution—powered by Stäubli robotics—addresses this by offering high-speed packing in a smaller footprint. Capable of packing hundreds of parts per minute, the system is designed to meet the specific needs of food processors.
The solution is fully customizable, allowing processors to adjust case design, palletizing styles, and product orientation. With a focus on minimizing downtime and maximizing output, EnSight’s system helps processors increase efficiency without requiring extensive space or resources.
Conclusion
As food processors face increasing demands for speed and efficiency, automation is becoming essential to remain competitive. EnSight Solutions’ compact, washdown-capable case-packing system offers a path forward for processors looking to streamline operations and improve productivity. With customization options and a focus on space-saving design, EnSight’s system addresses the challenges of modern food processing and helps companies achieve measurable results.
https://www.ensightsolutions.us/food_solution_category/robotics-automation/