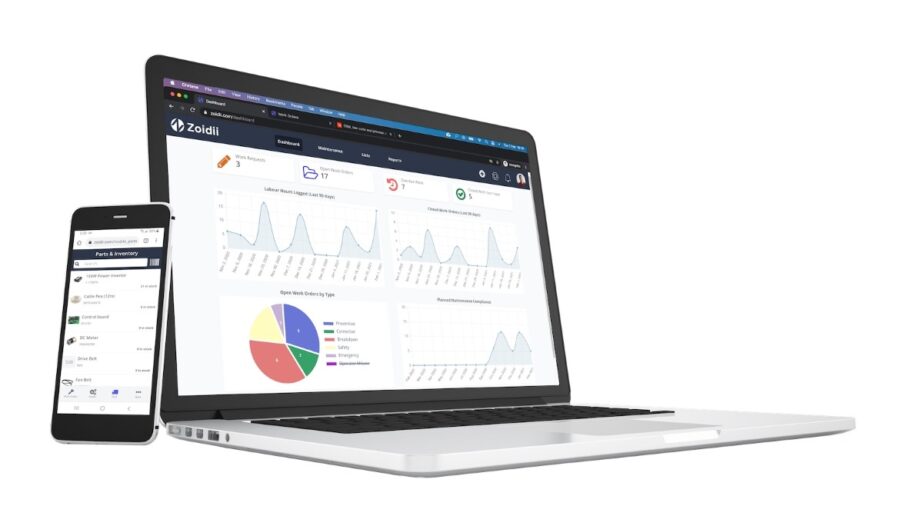
Image courtesy of Zoidii
7 Ways CMMS Software Benefits Food and Beverage Facilities in 2023
Today, food and beverage businesses constantly seek ways to optimize their operations and increase efficiency. One such solution that has gained significant traction is the implementation of Computerized Maintenance Management Systems (CMMS). There are various aspects of CMMS that are important to know before implementing it in your facility such as exploring its evolution, components, benefits and how to choose the right system for your organization.
What is a Computerized Maintenance Management System (CMMS)?
CMMS is a software application that centralizes and automates maintenance management tasks. CMMS software helps optimize the scheduling and tracking of maintenance work and provides data-driven insights to improve asset management and overall productivity. By digitizing maintenance records, organizations can more effectively monitor equipment performance and reduce operational costs.
A CMMS is an essential tool for organizations with production or facility assets that require regular maintenance. It helps to ensure that maintenance tasks are completed in a timely and efficient manner, reducing downtime, increasing productivity and increasing the lifespan of the equipment. Additionally, a CMMS can help organizations comply with regulatory requirements and improve safety by ensuring that equipment is appropriately maintained.
How do You Know if You Need CMMS Software?
Issues experienced by those organizations not using CMMS software include:
- It's difficult to report on maintenance performance
- No proper system to intake work requests at the facility
- Emergency breakdowns and idle line operators are common
- Maintenance costs fluctuate and are unpredictable
- Maintenance audits are difficult and time-consuming
How CMMS Software Works
CMMS software functions as a centralized repository for all maintenance-related data. It tracks and records information about each asset, including maintenance history, equipment specifications and spare parts inventory. Users can input work order requests, schedule preventive maintenance tasks and view detailed reports on asset performance, work orders and inventory levels. A CMMS helps organizations streamline their maintenance operations and make data-driven decisions by organizing and automating these processes.
Today, most organizations choose cloud-based CMMS when implementing new CMMS software. Cloud-based CMMS solutions require no expensive IT hardware and offer the advantage of being accessible from anywhere with an internet connection, including mobile devices. CMMS software is essential for any organization to optimize its maintenance operations and reduce costs. By centralizing and automating maintenance tasks, food and beverage facilities can improve asset management, reduce downtime and make data-driven decisions.
Benefits of Implementing a CMMS
Implementing a CMMS at your food and beverage facility can impact an organization's efficiency and bottom line. The following benefits are among the most commonly cited:
- Improved Asset Management
With a CMMS in place, organizations can optimize the care and management of their assets. The system provides vital information on equipment performance and maintenance history, enabling users to identify trends and potential issues. Access to valuable asset data helps maintenance folks make informed decisions that extend the lifespan of assets, reduce costly breakdowns and optimize resource allocation. - Streamlined Maintenance Processes
A CMMS streamlines processes and improves overall workflow by automating manual maintenance tasks and centralizing information. It eliminates the need for physical paperwork which in turn, reduces the likelihood of errors and ensures that technicians complete work orders in a timely manner—overall leading to a more productive and efficient maintenance team. - Enhanced Work Order Management
A key feature of a CMMS is the ability to manage work orders effectively. Users can easily create, prioritize, assign and track work orders, ensuring nothing falls through the cracks. It also boosts productivity and provides traceability for labor and resource allocations. - Reduced Downtime and Increased Productivity
A CMMS can significantly reduce unplanned downtime by maximizing the effectiveness of preventative maintenance tasks. Preventive maintenance minimizes the impact of equipment failures on productivity and ensures that assets are operating at peak performance. The ability to collect and analyze data related to asset performance is instrumental in identifying areas for improvement and addressing issues before they escalate. - Inventory Control
Effective inventory management is crucial for successful maintenance operations. With a CMMS, organizations can track spare parts inventory in real-time, reducing the risk of stockouts and ensuring that necessary parts are available when needed. Optimizing spare parts inventory in a CMMS can help reduce costs associated with excessive inventory and minimize the downtime caused by waiting for parts to arrive. - Data-Driven Decision Making
Lastly, a CMMS provides organizations with the data to make informed, strategic decisions. The system's reporting and analytics capabilities allow users to identify trends, and pinpoint areas for improvement by evaluating the effectiveness of their maintenance program. This data will enable organizations to optimize maintenance strategies and allocate resources more effectively. - Simplified Audits
Conducting audits can be daunting for food and beverage organizations due to the numerous local, regional, state, national and global compliance regulations to adhere to. However, the use of CMMS software can aid companies in complying with regulatory requirements by offering comprehensive maintenance records, schedules and reports. These records serve as digital proof during audits to demonstrate compliance. Essentially, CMMS software provides the digital trail that compliance audits often look for to evaluate a company's adherence to standards.
Critical Components of a CMMS
A well-designed CMMS incorporates several key components that contribute to its overall effectiveness. These typically include:
- Asset and equipment management
Asset and equipment management is a critical component of any CMMS. It allows organizations to track and manage their assets, including equipment specifications, maintenance history and warranty information. Organizations can make informed decisions about maintenance and replacement by having a complete view of assets.
- Work order management
Work order management is another critical component of a CMMS. It allows users to create, assign and track work orders, ensuring technicians complete maintenance tasks promptly and efficiently. Work order management can also help organizations prioritize tasks based on urgency and allocate resources more effectively.
- Maintenance scheduling
Maintenance scheduling is an essential feature of a CMMS. It allows organizations to schedule preventive maintenance tasks based on equipment usage and other factors, reducing the likelihood of equipment failure and downtime. Organizations can also reduce the administrative burden of managing maintenance tasks through automated schedules.
- Inventory and spare parts management
Inventory and spare parts management is a critical component of any maintenance operation. A CMMS can help organizations track inventory levels, order spare parts and manage stock levels. By having a comprehensive view of their inventory, organizations can reduce the likelihood of stockouts and ensure they have the necessary parts to complete maintenance tasks.
- Preventive and predictive maintenance
Preventive and predictive maintenance are key features of a CMMS. Preventive maintenance involves performing maintenance tasks regularly, while predictive maintenance involves using data to predict when the equipment will require maintenance. By combining preventive and predictive maintenance, organizations can reduce the likelihood of equipment failure and extend the lifespan of their assets.
- Reporting and analytics
Reporting and analytics are essential features of a CMMS. They allow organizations to track key performance indicators. An example could be reporting and analyzing equipment downtime and expected maintenance costs. With that information, organizations can make data-driven decisions.
Choosing the Right CMMS for Your Organization
Implementing a CMMS is a significant investment for any organization and choosing the right system for your specific needs is crucial. The following steps can help guide your decision-making process:
- Assessing Your Needs
Before you begin comparing CMMS options, it is essential to have a clear understanding of your organization's goals and requirements. Identify gaps in your current maintenance management processes, potential growth areas and the features and functions most important to your organization. This assessment will help narrow the list of potential CMMS vendors and guide product demonstrations.
- Comparing CMMS Features
Once you've identified your organization's needs, it's time to compare the features offered by different CMMS vendors. While most systems offer similar core functions, some vendors may provide additional features or specialize in specific industries or asset types. Consider your organization's requirements when examining additional features and how they may contribute to your maintenance management goals.
- Right Size the CMMS Software to your Business
It is crucial to tailor the software and implementation to the abilities of your business. If you intend to switch from manual methods to the most advanced Computerized Maintenance Management System (CMMS) that integrates with your Enterprise Resource Planning (ERP) system and equipment, ensure that you have the necessary resources to carry out the project and continually sustain the system.
- Evaluating Vendor Support and Training
Lastly, consider the level of support and training each CMMS vendor provides. Implementing a CMMS can be complex and adequate support and training are critical for a successful transition. Additionally, ongoing support ensures that your organization benefits from the system and can access help as needed. When comparing vendors, make sure to ask about support options, response times and the availability of training materials.
Implementing a CMMS at your food and beverage facility can benefit organizations looking to optimize their maintenance management processes. With the right system, businesses can streamline operations, improve asset management and make data-driven decisions. By carefully assessing your organization's needs and thoroughly evaluating potential CMMS options, you can ensure that you select the best solution to drive success and growth.