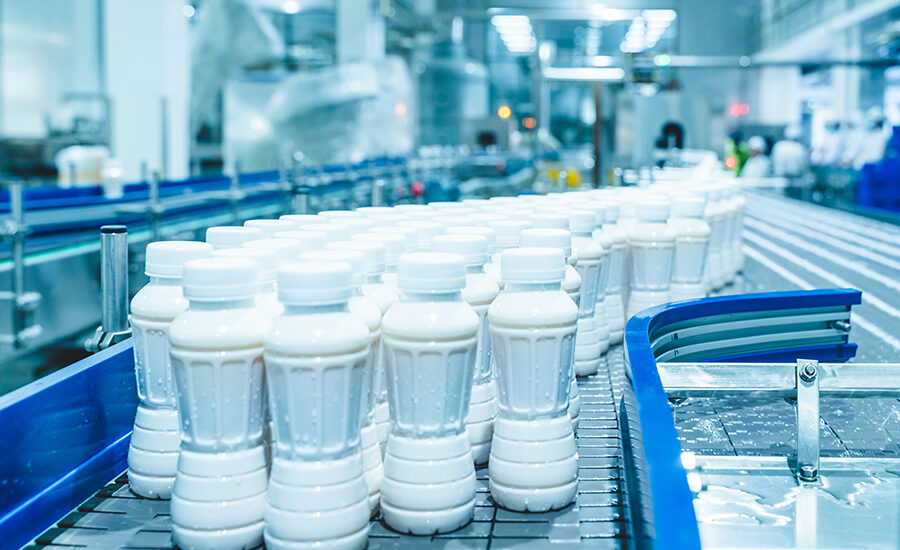
How to Navigate Conveying Trends in Food Packaging
Today’s transport systems can play an important role in making food packaging lines more energy efficient, more connected and more flexible than ever.
Material handling and transport is an essential operation in any food packaging line. But the conveyor systems used in these operations are often considered only for their ability to move products from point A to point B. Packaging lines that overlook the full potential of conveying technology may be missing out on solutions to some of their biggest challenges.
The food packaging industry today is a challenging environment: change is the only constant, sustainability is critical to survival, and demand for cost-efficient production is more exacting than ever. To gain an edge, packaging lines need to take advantage of every tool in their toolbox.
With the latest advances in conveyor technology, today’s transport systems can play an important role in making food packaging lines more energy efficient, more connected and more flexible than ever before. But how can food packagers navigate the wide range of technologies available to get the most from a new conveyor system?
We spoke with conveyor technology expert Justin Quattlebaum, a product manager for Bosch Rexroth, to learn how packaging lines can take advantage of the latest trends in conveyor technology.
FE: What are some of the top conveying needs you see in the food packaging industry? And what new trends and technologies can help?
Justin Quattlebaum: Energy consumption is a big concern for a lot of food packaging operations. They’re under pressure to not only meet ambitious sustainability goals, but also to optimize the cost of doing business. For conveyance, we’ve seen a lot of interest in getting away from pneumatics as much as possible because of the air consumption. But they’re also moving away from hydraulics and, whenever possible, they’re electrifying their systems.
This is an area where conveyors have seen a lot of improvements in the past 10 to 15 years. Today they have a very high drive-capacity, which allows greater conveyor lengths between motors or drives. And the gear motors are much more efficient. Stop gates can also improve energy consumption. There are a variety of electric stop solutions available today that can replace pneumatics in a variety of food packaging applications.
Food packaging lines also want more connectivity for better production transparency and data-driven decision making. What that looks like in practice can vary greatly depending on the needs of the operation. Some lines may need advanced built-in IoT capabilities and servo motors for things like instantaneous drive torque, or information about load on a conveyor per hour. For others, they need systems that can easily integrate with their IoT technology.
Modern conveyor systems can operate as the backbone of your IoT infrastructure, since the conveyor transports products from start to finish in the packaging line. And you don’t have to have the most expensive system for that to be true. There are plastic chain conveyor systems available today that are designed with connectivity in mind, with fixtures and other design features that make it easy to integrate sensors or mount cameras for real-time data capture.
FE: What kind of conveyor systems can give food packagers the most impactful benefits?
JQ: A big challenge in the food packaging industry that I failed to mention—because it almost goes without saying—is the constantly changing environment. Food packaging lines need maximum flexibility so they can quickly adapt to new packaging designs, portion sizes or entirely new product lines.
Having a modular conveyor system that can be easily assembled, reconfigured and expanded can make a huge difference in a line’s ability to quickly adapt to changing demands. Today there are modular chain conveyor systems available that don’t require any rivets, welding or machining to assemble, and they have an extensive range of components available to fit any kind of manufacturing footprint. This lets packaging operations quickly retool their lines if needed or expand capacity to meet shifting demand.
For high-volume operations, speed is also an important consideration. Linear motor-driven transfer systems today offer high precision and repeatability while delivering accelerations up to 4 g. This not only helps manufacturers reduce their cycle times, it also ensures more consistent quality in their products.
For high-volume operations, speed is also an important consideration. Linear motor-driven transfer systems today offer high precision and repeatability while delivering accelerations up to 4 g. This not only helps manufacturers reduce their cycle times, it also ensures more consistent quality in their products.
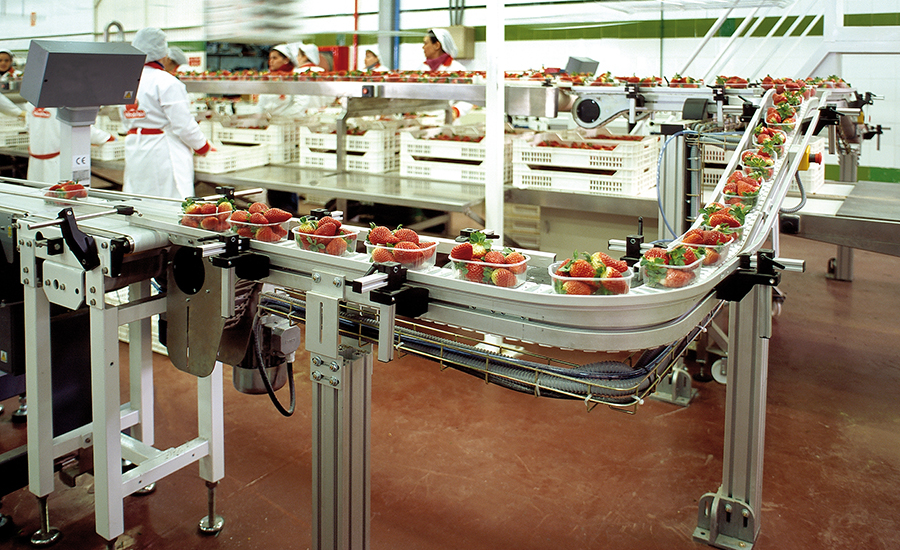
FE: For packaging companies looking to purchase a new conveyor system, how can they get the most from their investment?
JQ: The first piece of advice I would give to anyone designing a new system or upgrading an existing one would be to always keep an eye on the future. Will you need to add new machines or new technology? Do you plan to scale quickly? Will it be easy to maintain? These are critical considerations that food packaging operations need to plan for at the beginning. That means making sure runs are set to the right length, and that drives are placed with future expansion in mind so you don’t end up overloading a conveyor.
You also need to make sure that whatever system you go with can easily integrate into your existing infrastructure. That means looking at the whole portfolio to be sure the right widths, chain types and stop gates are available. Even if you’re just moving boxes, the conveying task is not always that simple. Sometimes you have to go up and down and around things, and that requires specific layouts, chain types and orientations to achieve it.
Also consider the human element and how a conveyor system will impact your workers on the floor. There are some very quiet, low-maintenance conveying options available that can help to improve your overall manufacturing environment and employee well-being.
FE: What should operations look for in a technology provider? And what level of partnership should they expect?
JQ: Food packaging operations will find the greatest advantages from a partner who can offer a complete technology portfolio, not just for conveying applications but for an entire production line. That will ensure you’re getting a conveyor system fit to your needs, and that it’s designed with the entire packaging line in mind. It will also ensure your conveyor system provider has the application expertise—should you need it—to help with planning, deployment and full lifecycle support.
A single-source provider can make a valuable partner for designing the whole production line. They’ll have the expertise to recommend turn-key solutions from their own portfolio or even third-party providers to make sure your production is at optimal performance.