Bulk bag handling for humanitarian food relief
Breedlove Foods Inc. increases its shelf-stable packages for humanitarian food relief with an automated bulk handling system from Flexicon
April 8, 2021
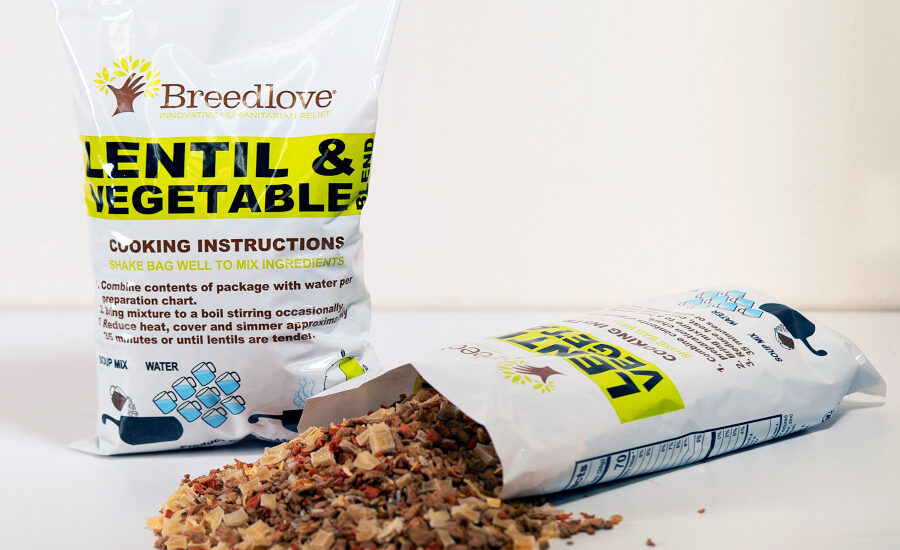
Breedlove Foods Inc., produces nutritious food products for humanitarian relief in the aftermath of hurricanes, earthquakes and other catastrophic events. The nonprofit company produces shelf-stable packages of ingredients such as lentils, rice, soy protein, dehydrated potatoes, onions and carrots. Packaged in 2.2 lb. (1 kg), 1.1 lb. (500 g) and 4.6 oz. (130 g) sizes, Breedlove’s food products require only water and 30 min. of cooking time.
The company installed an automated bulk handling system that boosted production of its Lentil and Vegetable Blend product more than sevenfold while improving worker safety. Two Flexicon Bulk-Out BFF bulk bag dischargers and six interconnected flexible screw conveyors distribute dehydrated lentils to four mixers, followed by packaging.
Purchasing lentils in bulk bags reduces ingredient costs, while discharging from bulk bags relieves workers of heavy lifting. “Operators were manually lifting five, 100 lb. (45.4 kg) bags of lentils and adding them to the mixers,” says Wesley Sloan, Breedlove’s maintenance team lead.
Automated bulk bag discharging of lentils
A forklift delivers a 2,000 lb. (908 kg) bulk bag of lentils from the warehouse to either of two side-by-side bulk bag dischargers and then positions a bag lifting frame immediately above the bag, allowing an operator to slide the bag’s four lifting straps into Z- Clip strap holders affixed to the lifting frame. The forklift then raises the frame with suspended bag and places it into receiving cups on the top of the discharger frame’s posts.
The operator then secures the clean side of the bag spout to the clean side of a Spout-Lock clamp ring positioned atop a Tele-Tube telescoping tube, which applies constant downward tension as the bag empties and elongates, to completely discharge lentils into the 20 cu. ft. (566 l) capacity hopper below. Spring-loaded Pop-Top extension arms on the discharger posts raise the bag as it lightens, further promoting discharge.
“With two bulk bag dischargers, we run one until it gets low and then run the other one,” says Sloan. “While No. 2 is running, operators are refilling No. 1 and there’s never downtime replacing product. Even with the 2,000 lb. (908 kg) loads in the work area, dust is not a problem.”
From each discharger’s floor hopper, a 20 ft. (6 m) long, 4.5 in. (114 mm) diameter flexible screw conveyor moves the lentils through an opening in the wall into the Packaging Room where they discharge into a 1 cu. ft. (28.3 l) capacity transition hopper atop a wye diverter valve that directs lentils into the four interconnected flexible screw conveyors feeding the four mixers. The conveyors, with lengths varying from 10 to 15 ft. (3 to 4.5 m), consist of a polymer tube enclosing a flat wire spiral driven by a 3 hp (2.25 W) motor beyond the discharge point, preventing material contact with seals or bearings.
Lentils exiting the conveyor are gravity fed through downspouting to one of four mixers where operators manually add minor dry ingredients, including rice, soy protein, potatoes, and onion. “Some recipes include 600 lb. (272 kg) of lentils from the bulk bag discharger, while many recipes and production runs are approximately 100 lb. (45.4 kg),” explains Sloan.
System operates under loss-of-weight control
At the control panel, the operator sets weight specifications and routing to a specific mixer. The batching system operates under loss-of-weight control whereby load cells supporting each discharger transmit weight loss data to a PLC, which runs a conveyor at high speed as material is discharged into a designated mixer. The PLC steps down the conveyor feed rate to dribble as the target weight is approached, stopping the conveyor once the precise batch weight has been lost from the discharger. “We’re getting excellent results from the system and are achieving our goal of below one percent for weight variants,” says Sloan. “Our rates are extremely accurate.”
Blended batches are discharged into a hopper that feeds its respective packaging machine, which outputs 2.2 lb. (1 kg), 1.1 lb. (500 g) or 4.6 oz. (130 g) packages.
Breedlove’s CEO Bill Miller says, “Before the packaging upgrades, Breedlove’s daily production averaged between 200,000 and 500,000 meal servings a day. Now, we can approach 1,500,000 meal servings a day. We have produced more than 22 million food servings for COVID-19 food relief, and the upgrades we completed played an integral part in that response.”
For more information, visit www.flexicon.com.