Equipment upgrade helps almond processor achieve gentle conveying sans air
Equipment upgrade helps almond processor achieve gentle conveying sans air
Hilltop Ranch installed a tubular drag cable conveyor system from Cablevey Conveyors to help process 50 million pounds of almonds annually
April 2, 2021
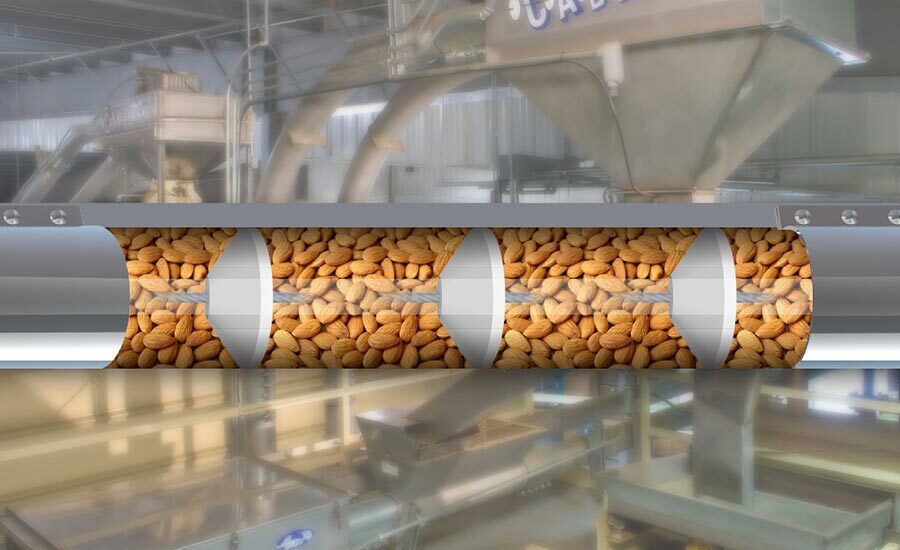
When Hilltop Ranch, a family-owned almond processing corporation in Ballico, Calif., decided to overhaul its processing line, it had to find an efficient way to move the almonds from point A to point B to point C in the plant, all while not causing damage to the nuts.
“One of the challenges we faced when planning the revamped processing line was how to transfer the almonds between various points in the plant while keeping them intact,” says Charlie Jahn, Hilltop Ranch’s quality manager.
One option for conveying the almonds is to use high velocity air power through tubes, bends or sweeps, but this can cause damage. For food processing companies with high-value product susceptible to damage—such as almonds—material breakage and loss is a very costly problem that can harm the bottom line. A difference between 1% waste and 5% waste can be the difference between profit and loss.
Jahn was looking for an enclosed conveying system that could make several pickups and drop-offs and be virtually dust-free. The system would have to fit the plant’s limited space, which was complicated by the addition of pasteurization equipment. Jahn experimented with aeromechanical and pneumatic conveyors, but both damaged the nuts unacceptably.
A gentler alternative to protect sensitive, high-value food products is a tubular cable conveyor, which can reduce product damage while improving cleanliness and production.
Totally Tubular
Tubular cable conveyor systems move product through a sealed tube using a coated, flexible stainless-steel drag cable pulled through on a loop. Solid circular discs (flights) are attached to the cable, which push the product at low speed through the tube without the use of air, preserving product integrity and minimizing waste. The approach can also enhance cleanliness and production in a minimal footprint.
After successful testing, Jahn implemented a tubular drag cable conveyor system from Cablevey Conveyors, Oskaloosa, Iowa.
According to Karl Seidel, marketing director at Cablevey Conveyors, these tubular conveyors are for products such as nuts, cereal, coffee, snacks, pet food, beans and seeds. The systems can convey up to 2,000 cubic feet per hour (56m3/hr.) of flakes, pellets, shavings, crumbles, granules, regrind, chunks, parts, prills and powders with numerous layouts using multiple inlets and outlets, he says.
Because the material is carried between the flights, it is easier to safely convey some easily compacted or sticky materials in a tubular cable conveyor than in air-powered conveying systems, where such materials can form plugs, Seidel adds.
Tubular drag cable conveyor systems also can help to prevent dust and fine granular product from escaping, which mitigates cross contamination and excessive cleaning.
Benefits Realized
The installation at Hilltop Ranch helped in several ways. During the revamped line’s first three months, the plant operated the conveying system for 1,400 hours. “The conveyors are working out very well,” says Jahn. “Compared to other systems we tried, they’re more dust-free and easier to clean, and they handle the almonds a lot more gently.”
The conveyor’s interchangeable components allow it to expand easily or to be reconfigured to change the length, conveying path and number of inlets and outlets. According to Seidel, these modifications are more complex and time consuming with a pneumatic conveying system, which has more components and electrical connections.
For more information, visit www.cablevey.com